Pellet mill maintenance
Sharp tools make good job. The maintenance of pellet mill will directly influence the quality of products and production efficiency. So it is necessary to maintain the high efficiency of pellet mill. Here are some suggestions for you.
Precautions
- Read the construction carefully before operation. Get familiar with its performance, structure and operating methods. Follow the instruction to install, test, use and maintain the mill.
- Know clearly about types of raw material you use. Get rid of anything hard in the raw material that may cause damage to the pellet mill.
- MUSTN’T put your hands in the transmission part or the hopper in case of unnecessary injury. Safety first.
- Cut the power down. For adjustment or maintenance of the pellet mill, for your safety, please turn off the power first.
- To avoid unexpected accident, the motor must equipped with effective grounded line.
Lubrication
- Spare parts of pellet mill including roller and die need to use lithium-based lubricants for daily maintenance, two times a day for regular lubrication.
- Gear box parts need to use hyperbolic gear oil lubrication to maintain its operation. Especially pay attention to the first time, the fuel need to join the specified location. And the lubrication is needed every 6 months.
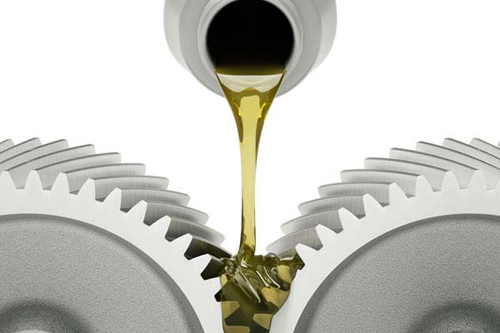
Maintenance
- Check the screws of different parts often to see if any of them slipping out. If it happens, take actions as soon as possible.
- Necessary measure should be taken to protect electrical parts from humidity, rain, corrosion, shock and damage. Ensure that the electrical box is clean and dry to keep away from electrical accidents.
- Check the roller and die often, any of them badly worn, change a new one to preserve its proper function.
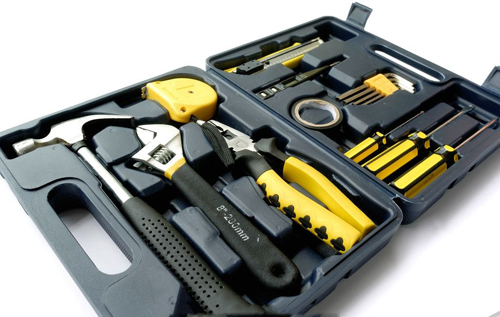
Cleaning
- To prevent the mill from being blocked, cleaning job is necessary after use every time.
- To prevent electrical problems such as short circuit or poor contact, the motor box should stay clean and away from dust, daily cleaning is needed.
- In order to facilitate the extension of service life, scattered materials should be cleaned immediately to keep the parts neat.
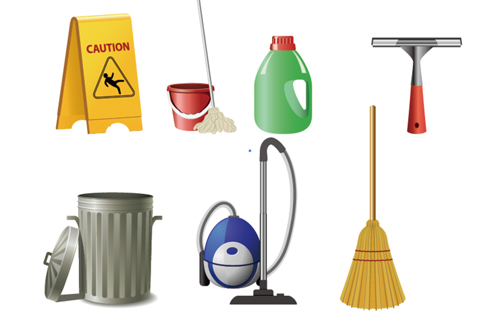
Malfunctions & Reasons & Solutions
Malfunctions | Reasons | Solutions |
---|---|---|
Low yield. | First time being used, the die holes are not smooth enough. | Use oil-bearing material to lubricate die holes. |
The raw material is either too wet or too dry. | Keep the raw material in correct moisture content. | |
The gap between roller and die maybe large. | Adjust the gap between roller and die. | |
Serious damage of spare parts. | Change new spare parts. | |
Unable to shape. | Low moisture content. | Improve the moisture content. |
Over-wear of die, and the compression is small. | Replace a new die. | |
Rough surface. | High moisture content. | Reduce the moisture content. |
A brand new die first time being used. | Use oil-bearing material to lubricate die holes. | |
Abnormal noise. | Hard foreign body like pebble falls into the mill. | Stop and move the foreign body away. |
Bearing broken. | Change the gear. | |
Looseness of spare parts. | Fasten spare parts. | |
Impurities in gear oil which cause damage to the gear. | Check the gear or contact the manufacturer directly. |